We had the opportunity to sit down with Rich Krueger to talk about Standard Electric's Enclosure Modification services and his roles as Mod Shop Manager and Application Specialist. Here's what he had to share...
Tell us about your role with Standard Electric...
Most of the enclosure modifications done at Standard Electric are coordinated by me because I manage the mod shop facilities in Sheboygan and Chicago Ridge.
I work closely with two independent mod shops, same goes for painters. We have two different painters we work with, and keep in close contact in case we have to do any custom paint colors. We also have a couple different fabricators that will manufacture parts for us if it’s something custom or it’s something that we can do locally because its quicker and sometimes cheaper.
Standard Electric's Enclosure Modification services range in their complexity. What else can you tell us about these services and how you ended up with this engineering focus?
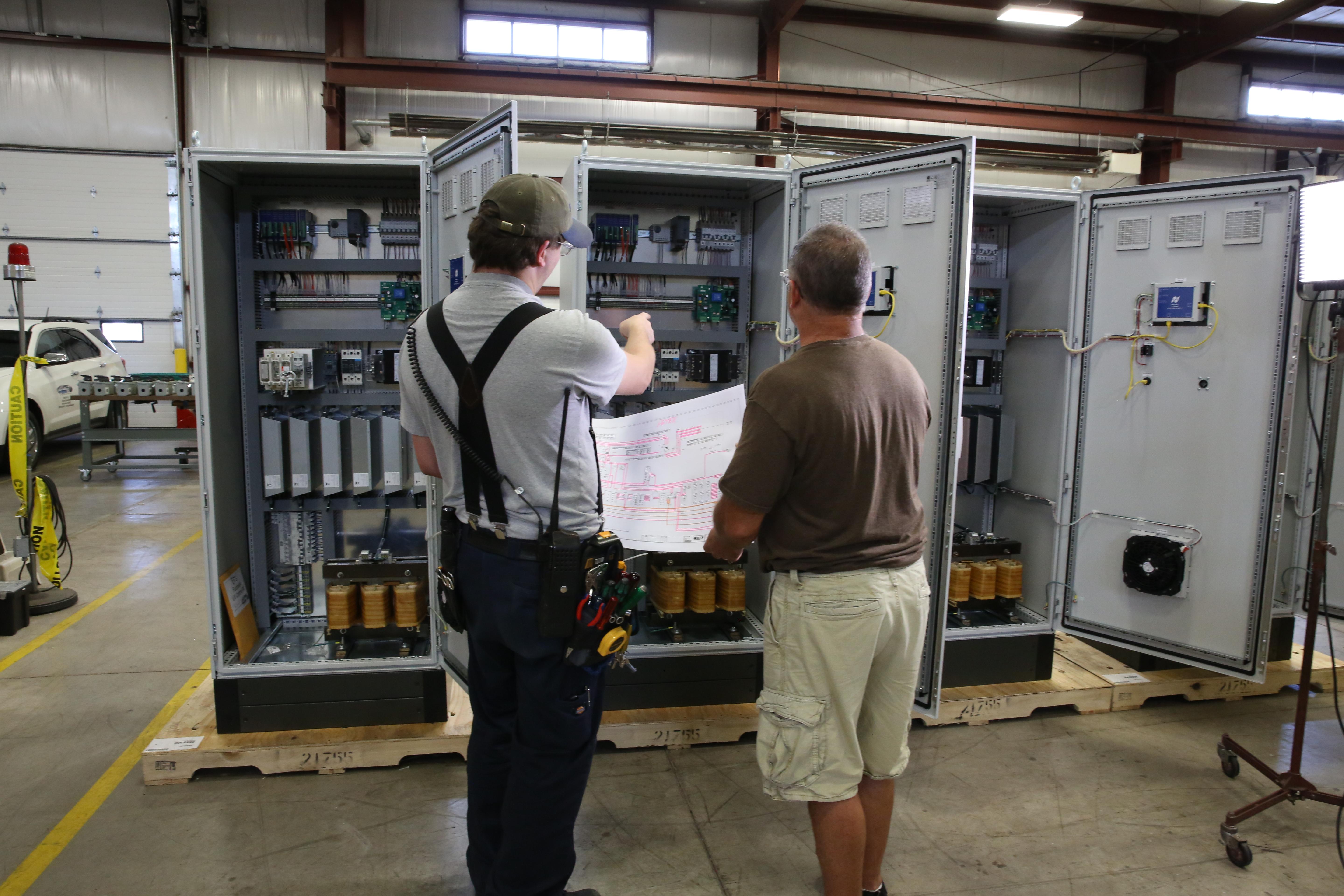
We do a lot of assemblies, cut outs, and drilling and tapping mounting panels. That’s the day in and day out basic stuff. The biggest part of engineering focus for me is when customers have a greater challenge for how they plan to utilize their enclosures.
For instance, have one customer who needs their enclosure hinged on the top. Since it’s a large wall mount, you run into the problem of how to open the extremely heavy door and keep it up. The customer said he's been working with a factory and they don’t have a solution. That’s where I pride myself on having the knowledge to see and be able to solve this problem. In this case, I thought of something similar to a hatch back car, where these hydraulic cylinders aid in lifting the trunk and holding it up while you get your groceries out of the car and then close it.
We had another customer that had a problem lifting their enclosures up. They said every time they tried to pick them up, the enclosures shifted around. Each enclosure is approximately six feet wide and three of them were suited together. They were picking it up right where the enclosures were suited together. The problem was that the enclosure needed support on the bottom as they were being picked up from the top. I envisioned and created an underneath structure to hold the enclosure together and make it safer to move.
How have you been able to learn and grow in your role?
I have always found it extremely important that you understand the scope of a project. When I’m working with our associates in the mod shops, I’m always asking them what we have done so far and what do we have left to do so I understand exactly where we are in the project. I don’t manage from sitting behind a desk, I prefer to be hands-on and active in the day to day operations.I feel it is extremely important to get people to understand that what we do is not difficult, but it takes time. If the enclosure is small enough where we can pick it up and lay it on a table to put the base on it, that’s great. For an enclosure that is wider, we have to put straps on it and use the forklift to pick it up because there is no safe way to lay this enclosure down due to its size and weight. Is it difficult to put that base on? No, not really, but it probably takes a half hour to do.
What do you wish more customers knew about enclosure modification services?
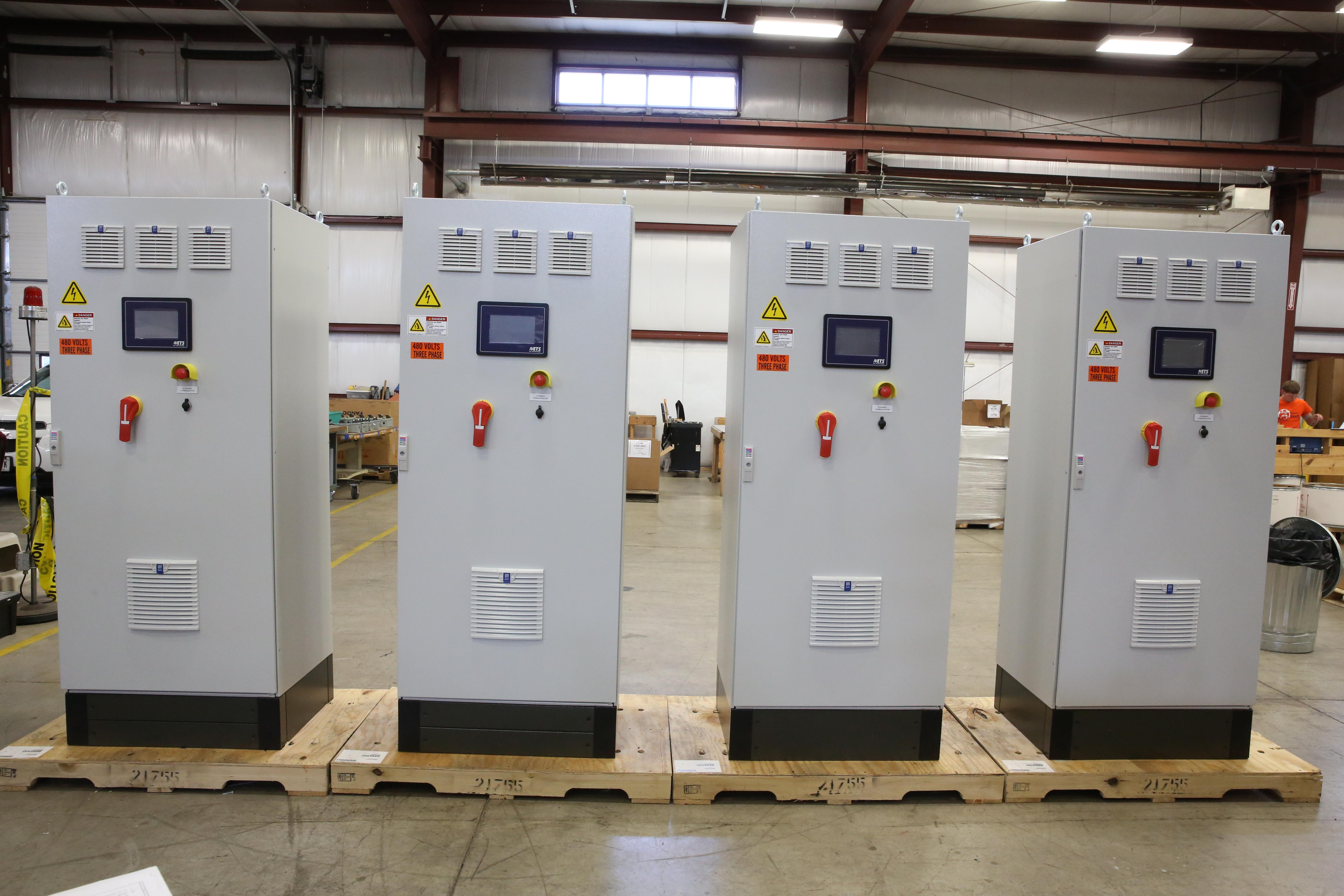
For the customer, it’s a matter of letting the party do the work they’re best suited for in order to keep the project moving as quickly and efficiently as possible.
What's the most rewarding part of your job?
The part I enjoy the most about what I do is being able to see the projects come together. While I can envision what it looks like in my mind, it’s nice to actually see the completed picture. Last week we had about 10 assemblies that we were working on and on Thursday afternoon I was able to send all three Account Managers involved an email around 4:00 PM to let them know that everything was completed. To see the shop floor go from completely filled to loading up a semi and seeing the stuff go is a huge feeling of accomplishment to me.Standard Electric Supply Co. is a family-owned distributor, built on delivering outstanding service. For over 100 years, Standard Electric has been the best at what they do; delivering top-quality products, outstanding service, and providing value-added services to customers across the Midwest. Visit standardelectricsupply.com to see how Standard Electric can become the solution to your needs.